Графитот е вообичаен неметален материјал, црн, со отпорност на високи и ниски температури, добра електрична и топлинска спроводливост, добра подмачкувачка способност и стабилни хемиски карактеристики; добра електрична спроводливост, може да се користи како електрода во EDM. Во споредба со традиционалните бакарни електроди, графитот има многу предности како што се отпорност на високи температури, мала потрошувачка на празнење и мала термичка деформација. Покажува подобра прилагодливост во обработката на прецизни и сложени делови и електроди со големи димензии. Постепено ги заменува бакарните електроди како електрични искри. Главен тек на машинските електроди [1]. Покрај тоа, графитните материјали отпорни на абење можат да се користат под услови на голема брзина, висока температура и висок притисок без масло за подмачкување. Многу опрема широко користат клипни чаши, заптивки и лежишта од графитен материјал.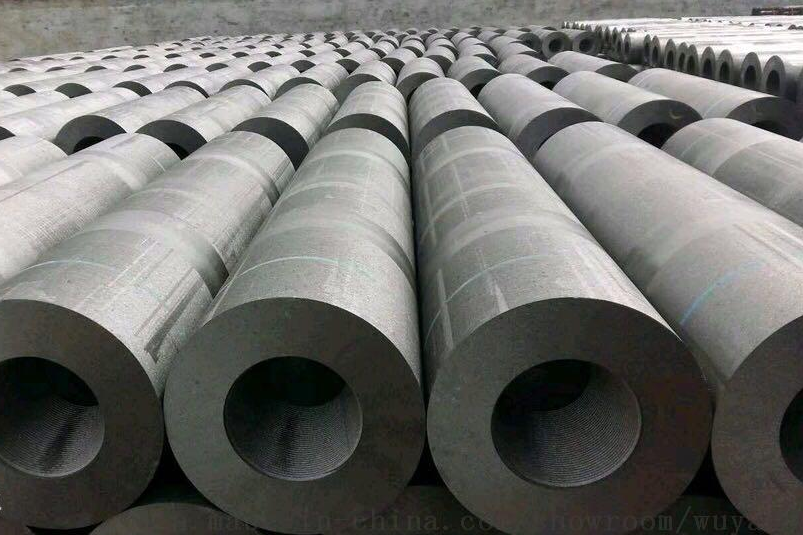
Во моментов, графитните материјали се широко користени во машинската, металуршката, хемиската индустрија, националната одбрана и други области. Постојат многу видови графитни делови, сложена структура на делови, висока димензионална точност и барања за квалитет на површината. Домашните истражувања за обработка на графит не се доволно длабоки. Домашните машински алатки за обработка на графит се исто така релативно малку. Странските машини за обработка на графит главно користат центри за обработка на графит за брза обработка, што сега стана главна насока на развој на обработката на графит.
Оваа статија главно ја анализира технологијата на обработка на графит и машинските алати за обработка од следниве аспекти.
①Анализа на перформансите на обработка на графит;
② Најчесто користени мерки за технологија за обработка на графит;
③ Најчесто користени алатки и параметри за сечење при обработка на графит;
Анализа на перформансите на сечење графит
Графитот е кршлив материјал со хетерогена структура. Сечењето на графитот се постигнува со генерирање на дисконтинуирани честички од струготини или прав преку кршливо кршење на графитниот материјал. Во врска со механизмот на сечење на графитните материјали, научниците дома и во странство направиле многу истражувања. Странските научници веруваат дека процесот на формирање на графитни струготини е приближно кога сечилото на алатот е во контакт со обработуваното парче, а врвот на алатот е згмечен, формирајќи мали струготини и мали вдлабнатини, и се создава пукнатина, која ќе се прошири на предниот и долниот дел од врвот на алатот, формирајќи вдлабнатина, а дел од обработуваното парче ќе се скрши поради напредувањето на алатот, формирајќи струготини. Домашните научници веруваат дека графитните честички се исклучително фини, а сечилото на алатот има голем лак на врвот, па затоа улогата на сечилото е слична на екструдирањето. Графитниот материјал во контактната површина на алатот - обработуваното парче е притиснато од површината на греблото и врвот на алатот. Под притисок, се создава кршливо кршење, со што се формираат струготини [3].
Во процесот на сечење графит, поради промени во насоката на сечење на заоблените агли или агли на работниот дел, промени во забрзувањето на машинската алатка, промени во насоката и аголот на сечење во и надвор од алатот, вибрации при сечење итн., се предизвикува одредено влијание врз работниот дел од графитот, што резултира со работ на графитниот дел. Кршливост на аглите и кршење, сериозно абење на алатот и други проблеми. Особено при обработка на агли и тенки и тесноребрести графитни делови, поголема е веројатноста да се предизвикаат агли и кршење на работниот дел, што исто така стана тешкотија при обработката на графит.
Процес на сечење на графит
Традиционалните методи на обработка на графитни материјали вклучуваат стругање, глодање, брусење, пилање итн., но тие можат да ја реализираат обработката само на графитни делови со едноставни форми и ниска прецизност. Со брзиот развој и примена на графитни центри за обработка со голема брзина, алатки за сечење и сродни потпорни технологии, овие традиционални методи на обработка постепено се заменуваат со технологии за обработка со голема брзина. Праксата покажа дека: поради тврдите и кршливи карактеристики на графитот, абењето на алатот е посериозно за време на обработката, затоа се препорачува употреба на алатки со карбидна или дијамантска обвивка.
Мерки за процесот на сечење
Поради специфичноста на графитот, за да се постигне висококвалитетна обработка на графитните делови, мора да се преземат соодветни процесни мерки за да се обезбеди. При груба обработка на графитниот материјал, алатот може директно да се напојува со работниот дел, користејќи релативно големи параметри на сечење; за да се избегне кршење за време на завршната обработка, често се користат алатки со добра отпорност на абење за да се намали количината на сечење на алатот, и да се осигура дека чекорот на алатот за сечење е помал од 1/2 од дијаметарот на алатот, и да се извршат процесни мерки како што е обработка на забавување при обработка на двата краја [4].
Исто така, потребно е разумно да се организира патеката на сечење за време на сечењето. При обработка на внатрешната контура, околната контура треба да се користи колку што е можно повеќе за да се сече присилниот дел од исечениот дел секогаш да биде подебел и поцврст, и да се спречи кршење на обработуваниот дел [5]. При обработка на рамнини или жлебови, изберете дијагонално или спирално полнење колку што е можно повеќе; избегнувајте острови на работната површина на делот и избегнувајте сечење на обработуваниот дел на работната површина.
Покрај тоа, методот на сечење е исто така важен фактор што влијае на сечењето на графит. Вибрациите на сечењето за време на глодањето надолу се помали од оние при глодањето нагоре. Дебелината на сечењето на алатот за време на глодањето надолу се намалува од максимумот на нула, и нема да има феномен на отскокнување откако алатот ќе сече во работниот дел. Затоа, глодањето надолу генерално се избира за обработка на графит.
При обработка на графитни парчиња со сложени структури, покрај оптимизирањето на технологијата на обработка врз основа на горенаведените размислувања, мора да се преземат и некои посебни мерки според специфичните услови за да се постигнат најдобри резултати од сечењето.
Време на објавување: 20 февруари 2021 година